Tajne fabrike Kru, gde se rađa luksuz Bentlija
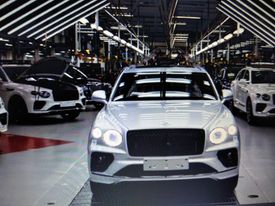
Uvek smo bili skloni povezivanju veoma dugih proizvodnih procesa sa luksuznim automobilima, uglavnom zanatskim i sa veoma ograničenim količinama. Pa, zapravo je tako, tačnije, samo delimično. Bentli i u ovom slučaju fabrika u Kruu u Engleskoj predstavljaju izuzetak od pravila.
Ovde se rađaju svi modeli “B Alata” u cenovniku: svi proizvedeni sa pažnjom i zanatskom pažnjom od strane specijalizovanih tehničara i zanatlija. Sve to, međutim, začinjeno tehnologijom i iskustvom u proizvodnim procesima Volksvagen grupe koja od 1998. godine poseduje Bentlei. Išli smo da vidimo kako to funkcioniše i takođe vam to objašnjavamo na video snimku.
Svi automobili u jednoj fabrici
Među zelenim predelima okruga Češir, četrdesetak minuta vožnje automobilom od Mančestera, nalazi se veliki industrijski centar sa tipično engleskim ukusom. Sve zgrade su prekrivene crvenim ciglama, a veliki prozori vam omogućavaju da zavirite u unutrašnjost fabrike u kojoj se rađaju neki od najluksuznijih automobila na svetu: Bentliji.
Ovde se proizvode Continental GT , Fliing Spur i Bentaiga , koji danas sami čine skoro 45% ukupne prodaje brenda. Upravo da bi se izborila sa ovim ogromnim porastom obima (samo pomislite da se do 2000. godine proizvodilo 700 automobila godišnje, a danas imamo 14.000 automobila), fabrika je duboko modernizovana kombinovanjem tradicionalnijih proizvodnih procesa sa savremenim tehnikama i novim tehnologijama.
Sve domaće, ili skoro
Proputovali smo dužinu i širinu Bentaiga proizvodne linije. Ovo, uz 90 različitih radnih stanica, dovodi do stvaranja četrdesetak primeraka dnevno. Sve počinje dolaskom leševa u fabriku. Oni se prave u drugoj fabrici, a zatim se šalju ovde u Creve. Dok se farbaju (potrebno je 5 do 7 dana da se nanese pet slojeva boje potrebnih za završetak procesa), pogonski sklop se sklapa u drugom delu.
Vozeći Bentlei modele su hibridni V6, V8 i legendarni V12 . Od ova tri, međutim, samo V12 se proizvodi interno u Kruu, duž namenske proizvodne linije. Ostali se sklapaju u Nemačkoj i zatim šalju ovde da bi se ugradili u automobile.
Pobuna drveta i kože
Ali najzanatskiji deo celokupnog proizvodnog procesa je onaj koji se tiče enterijera i posebno izrade presvlake od drveta i kože. Prve stižu iz različitih delova sveta i nakon laserskog rezbarenja nanose se na aluminijumske ploče da bi ih zatim ručno obrađivali specijalizovani tehničari, koji ovim komponentama daju završnu obradu koju želi kupac.
S druge strane, kože potiču od skandinavskih bikova i zatim se štave u Italiji, pre nego što stignu ovde u Kru, gde se, nakon sečenja, ručno šiju da pokriju kontrolnu tablu, panele vrata i sedišta. Zamislite samo da je potrebno preko 130 metara konca za šivenje svih enterijera Bentaige . Ali ono što je najupečatljivije pri ulasku u ove delove establišmenta su mirisi, odnosno parfemi. Tople note drveta i kože su dominantni mirisi ovde, u oštrom kontrastu sa onima koji se obično percipiraju u fabrici automobila.
Budućnost je nula uticaja
Ukratko, tradicija se susreće sa inovacijama u fabrici Creve. Za proizvodnju jednog automobila potrebno je oko 130 sati , u kojem se visokotehnološki sati povezani, na primer, sa proizvodnjom motora V12, dodaju drugim satima koje su više zanatlije vezane za kreiranje enterijera.
A u međuvremenu, pogon britanskog Bentlija nastavlja da raste, ne toliko po veličini koliko u tehnologiji. Da bi se postigao cilj dekarbonizacije postavljen za 2030. godinu, u fabrici su već izabrana zelena rešenja: postoji mnogo solarnih panela u celoj fabrici, koji mogu da garantuju više od 10 MVh energije godišnje. A u budućnosti će se povećavati održiva rešenja vezana za proizvodnju, upravo da bi pratili proces elektrifikacije asortimana koji će do 2030. godine biti lansiran sa pet novih potpuno električnih modela.