Otkrivamo vam koliko je suluda proizvodnja najskupljeg BMV-a ikada
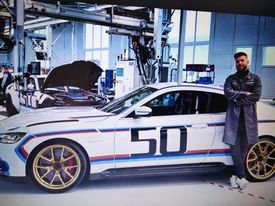
BMV 3.0 CSL je šlag na torti za 50 godina M divizije . Proizveden u samo 50 jedinica, to je omaž istoimenom automobilu koji je dominirao panoramom evropskog motosporta 70-ih zajedno sa legendama kao što su Kris Amon i Niki Lauda. Trebalo bi da košta 750.000 evra . Uslovna kazna je neophodna jer cifra nije potvrđena, ali portparol M odeljenja Martin Šlipen podsmešljivo ističe: „Nismo čak ni demantovali tu cifru, zar ne?“
Da bi objasnili razlog ove cene, koja ga čini najskupljim serijskim BMV-om svih vremena, bavarska kuća je dozvolila nekim novinarima, uključujući Motor1.com, da pogledaju proizvodnju. Evo kako je to prošlo.
Faza 1: lakiranje
Čini se čudnim, ali boja 3.0 CSL već daje prvu ideju zašto ovaj automobil toliko košta. Nalazimo se u Nemačkoj , u fabrici komponenti Landshut. Ovde 3.600 zaposlenih proizvodi električne motore, kokpitove i 500.000 ugljeničnih delova godišnje. To je takođe farbara za BMV 200 pojedinačnih nijansi boja . Ovde se svake godine ofarba 14.000 serija automobila koji se zatim šalju u fabrike u Minhenu, Lajpcigu ili Regensburgu.
Za 3.0 CSL odlučeno je da se ručno ofarbaju tri M-tipične trake u tamnoplavu, svetloplavu i crvenu. Trebalo je godinu dana da se planira proces , uključujući izradu alata. Za svaki automobil uključeno je 20 delova karoserije (većina ugljenika). Neki od njih su veoma neobični. „Kada je dizajner nacrtao i pruge na ušici kuke za vuču, bili smo zadivljeni – kaže Koh –. Ali uspeli smo i to”.
Sve zahvaćene delove robot prvo ofarba u tamno plavu – boju centralne M-trake. Zatim se tamnoplava traka “maskira” i nanosi crvena i plava. Zatim se i ove pruge maskiraju i robot farba ceo deo u belo. Na kraju se nanosi prozirni lak. Ukupno ima sedam slojeva laka . Između, naravno, uvek je brušenje. Potrebno je nedelju dana da se komad potpuno završi.
Samo četiri ili pet zaposlenih u celoj fabrici mogu da rade ručno farbanje . „Neki radovi na farbanju se odvijaju u milimetarskom opsegu, što je neophodno za postizanje savršenog rezultata“, objašnjava Koh.
Da bi se osiguralo da ovo uspe, komponenta koju treba farbati je pričvršćena na postolje. Pored nje, radnik blokira repliku obližnje komponente koja će se farbati. Ovo dolazi od 3D štampača. U ovom trenutku, laser pokazuje tačno kako treba da izgledaju pruge. Zatim se nanosi odgovarajuća folija prema laserskom obeležavanju . Za svaku komponentu postoji do deset pojedinačnih folija. Zatim moler skida unapred isečene folije tačno na trakama i počinje da slika. Za natpis “50” na krovu ili “M Pover” na zadnjem krilu, karbonski je maskiran i obojen samo u belo.
Sama hauba vredi pet cifara, kaže Koh. A zašto je svih 50 primeraka 3.0 CSL belo? Zbog uključenih procesa, koji inače ne bi bili mogući. Štaviše, ovo su klasične BMV boje za moto sport.
Faza 2: proizvodnja karoserije i enterijera
Da biste videli kako se vešto ofarbani delovi pretvaraju u automobil, morate se preseliti u Moosthenning . Ova MINI fabrika je najmanji satelit fabrike Dingolfing, koja je najveća BMV-ova u Evropi. Ovde 17.000 zaposlenih napravi 245.000 automobila godišnje. U Moostheningu proizvode malo manje, tačno jedan dnevno . Trideset zaposlenih ovde sklapa 3.0 CSL.